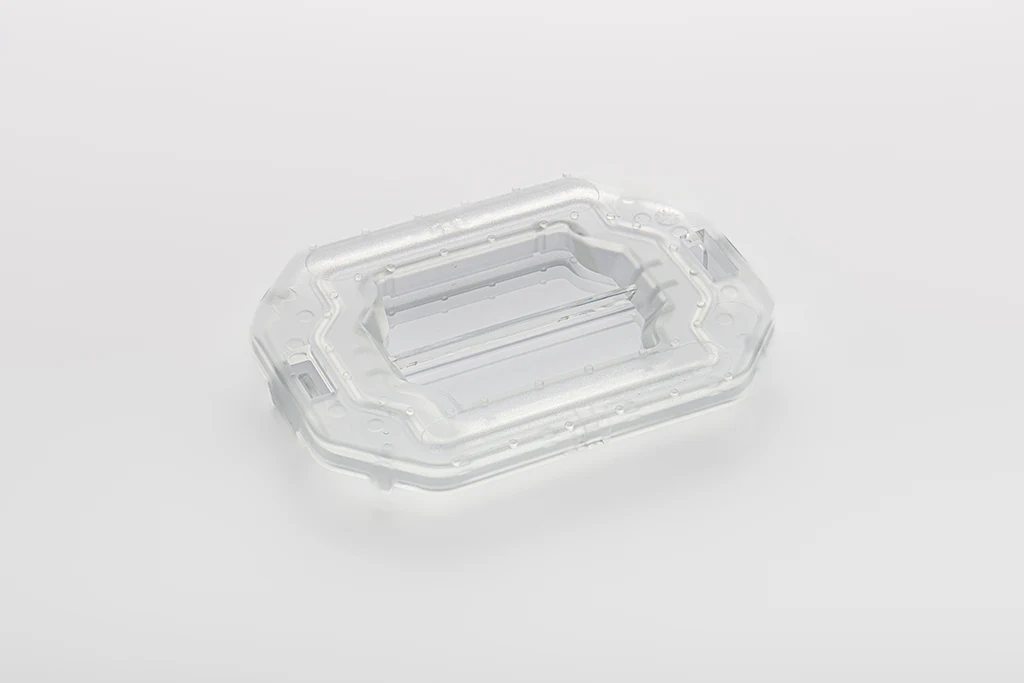
Product development
Product development at Murrplastik Medizintechnik takes place under strict clean room conditions (ISO class 7) in the subsequent manufacturing process to ensure that the medical technology products manufactured meet the highest quality and hygiene standards. This ensures the safety and effectiveness of the injection molded components and assemblies produced.
Concept and design
Product development begins with the conception and design of new medical products. This includes the identification of requirements and specifications in close cooperation with medical experts and customers.
Material selection
Materials are selected that meet the high standards of medical technology. These materials must be biocompatible and sterilizable to ensure patient safety and product quality.
Risk management
The identification and assessment of risks is an important aspect for the validation of medical devices. This is a practiced process at Murrplastik Medizintechnik and helps to minimize potential hazards and implement risk mitigation measures.
Prototype development: Prototypes are needed to extensively test the functions and requirements in the production of the subsequent series articles under clean room conditions.
Validation
At the beginning, a comprehensive validation plan is drawn up that defines the specific objectives, methods, responsibilities and phases (DQ; IQ; OQ; PQ) for the validation. This plan is drawn up in accordance with the applicable regulations and standards (MDR; FDA: etc.).
Documentation and certification
All steps in the development and production process are carefully documented to ensure product traceability. In addition, the products are certified in accordance with the applicable regulations and standards (MDR; FDA; etc.).